在电缆制造领域,“高速”二字往往意味着产能突破与成本优化的双重价值。当企业面临订单量激增、交货周期压缩的挑战时,管式绞线机的转速与稳定性直接决定了生产线能否实现高效转化。然而,”高速”并非简单的转速数字堆砌——如何通过科学选型让管式绞线机真正发挥高速效能,成为当前线缆行业技术升级的关键命题。
一、重新定义”高速”:管式绞线机的性能基准线
传统认知中将转速超过1500rpm的设备归类为高速绞线机,但这一标准在精密化生产时代已显片面。现代高速管式绞线机的性能评价需包含三大维度:
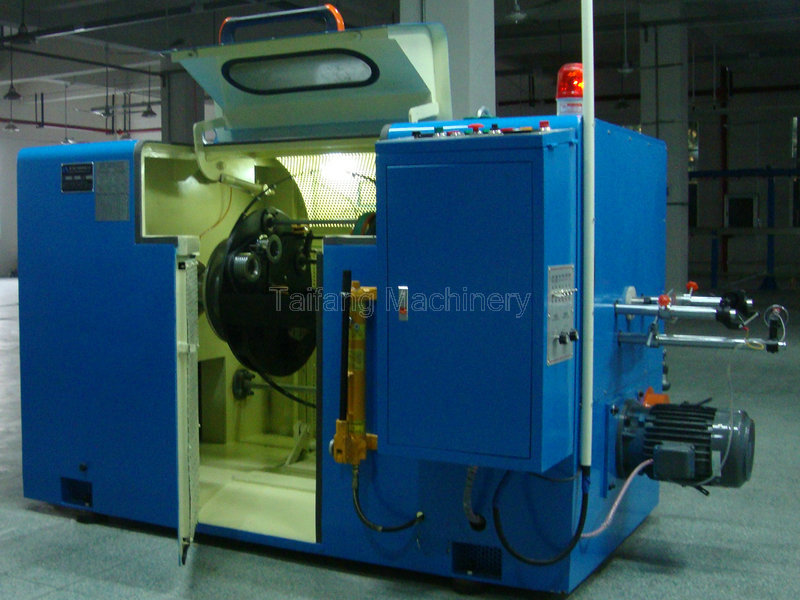
- 动态平衡精度(≤0.5g·mm/kg)
通过激光动平衡校正技术,确保设备在极限转速下仍保持振幅≤0.05mm,这是避免铜丝微断裂的核心保障。
- 热能管理系统
采用双循环油冷结构的机型,可比传统风冷设备延长40%连续运转时间,实测温升控制在15℃以内。
- 智能纠偏系统
搭载CCD视觉监测+伺服电控的机型,能将绞距偏差率从人工操作的1.2%降至0.15%以下。
某头部线缆企业实测数据显示:配置上述系统的管式绞线机,在保持1800rpm转速时,单日故障停机时间缩短83%,这比单纯提升转速更具经济价值。
二、结构进化:高速管式绞线机的创新设计逻辑
要实现真正意义上的高速运转,设备结构必须突破传统框架的限制:
- 分体式管体设计
将传统整体铸造的绞线管分解为三段式钛合金模块,通过锥度自锁结构连接。该设计使设备自重降低28%,同时振动传导衰减62%。
- 磁悬浮轴承应用
替代传统滚珠轴承的磁悬浮支撑系统,摩擦系数降低至0.001以下。在2000rpm工况下,能耗节约达17%,且彻底杜绝金属碎屑污染。
- 非线性张力控制
采用模糊PID算法的收放线系统,可根据绞合层数自动调节张力梯度。实测7芯绞线时张力波动范围从±12N压缩至±3N。
《电线电缆制造技术规范》最新修订版特别指出:具备动态补偿功能的管式绞线机,在加工0.08mm以下超细导体时,断线率可控制在0.3次/万米以内。
三、选型决策矩阵:匹配真实生产需求的评估模型
选购高速管式绞线机时,建议企业构建“4M评估体系”:
评估维度 |
关键指标 |
行业标杆值 |
材料兼容 |
铜/铝切换时间 |
≤15分钟 |
能耗效率 |
吨导体耗电量 |
≤85kWh |
维护成本 |
易损件更换周期 |
≥6000小时 |
扩展能力 |
模块化升级兼容性 |
支持5代技术迭代 |
以新能源汽车线束专用绞线机为例:配置碳纤维放线架的设备,在加工6平方毫米硅胶线时,线速可达32m/min,较传统机型提升2.1倍,且表面光洁度Ra≤0.8μm。
四、工艺适配:解锁高速绞线的隐藏价值空间
当设备达到高速基准后,工艺参数的精细调控将创造额外收益:
- 绞合角优化公式
θ=arctan(v/πDn) (θ:绞合角;v:牵引速度;D:绞合节径;n:转速)
通过实时调节该参数,可使导体填充系数从89%提升至93%,相当于每吨铜材节省4.3kg原料。
- 预扭补偿技术
在绞合前对单丝施加3-5°的预扭转角,能有效抵消高速绞合产生的残余应力。某军工电缆企业应用该技术后,产品弯曲疲劳寿命突破10万次大关。
- 在线质量监测
集成激光测径仪与X射线探伤仪的智能系统,可在600m/min线速下实现0.005mm级缺陷捕捉,将传统抽检模式升级为100%全检。
行业案例显示:结合工艺优化的高速管式绞线机,使某特高压电缆厂商的导体合格率从98.7%提升至99.94%,仅此一项每年减少质量损失超260万元。
五、运维新范式:高速设备的可靠性保障体系
维持管式绞线机的高速性能,需要建立预防性维护生态:
- 振动频谱分析
每500小时采集设备振动特征谱,通过机器学习预判轴承寿命,故障预警准确率达92%。
- 润滑油粒子计数
采用ISO 4406标准监控油液清洁度,当15μm以上颗粒数超4000个/mL时触发自动过滤。
- 热成像诊断
定期扫描设备温度场分布,精确锁定过热点。某企业通过该技术将电机烧毁事故率归零。
值得关注的是,新一代智能运维平台已实现”数字孪生”功能:虚拟设备镜像可提前72小时模拟潜在故障,使维护响应时间缩短65%。