“操作视频看十遍,不如师傅带一遍?” 在塑料管材生产领域,这句流传多年的俗语正被数字化浪潮改写。随着PP(聚丙烯)管材在建筑给排水、化工输送等场景的广泛应用,挤出机操作工艺的标准化需求日益迫切。一组行业数据显示:2023年因操作不当导致的PP管材废品率高达7.2%,直接经济损失超15亿元。此时,专业级PP管挤出机操作视频正成为破解这一困局的关键钥匙。
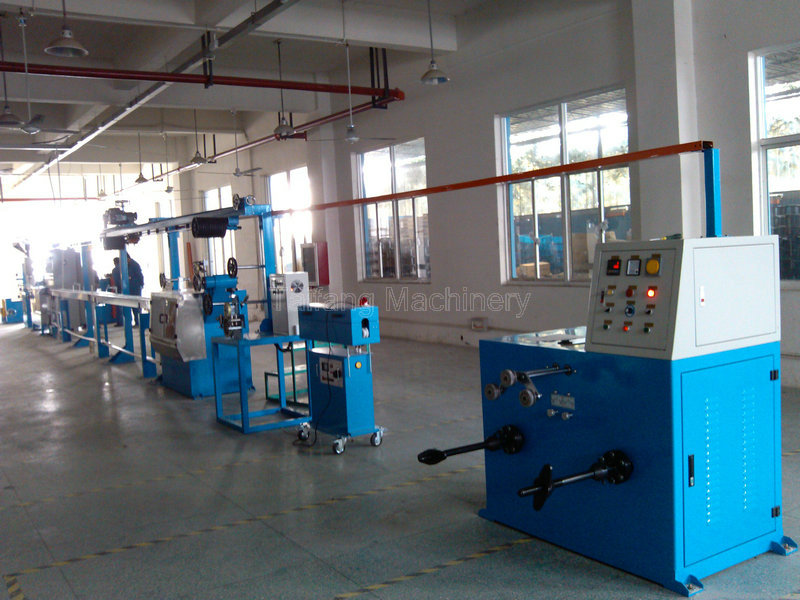
一、为什么需要专业操作视频?
在传统生产车间,操作工多依赖师徒传承经验,但人工传授存在三大痛点:参数记忆偏差、操作细节遗漏、应急处理经验断层。某卫浴管材生产企业曾因工人误将挤出温度设定低10℃,导致整批管材出现螺旋纹缺陷。而系统化的操作视频能完整呈现温度控制区段、螺杆转速匹配、模头压力监测等23项核心参数标准。
目前主流视频内容涵盖三大模块:
- 基础操作流程(设备预热→原料投放→参数设定)
- 异常工况处置(堵料处理→温度异常报警→紧急停机程序)
- 设备维护规范(螺杆清洁周期、齿轮箱润滑要点)
二、挤出机操作全流程拆解
1. 开机准备阶段
- 温度分区预热:根据PP原料型号(如PPR80、PPB)设定5-7段加热区,通常机筒温度控制在190-230℃
- 螺杆低速空转:转速≤15rpm,持续3-5分钟至出料口无黑斑
- 真空校准:确保定径套真空度稳定在-0.06~-0.08MPa
2. 生产运行监控
- 关键参数黄金比例:
- 挤出压力:18-25MPa
- 牵引速度=挤出速度×1.02-1.05
- 冷却水温度:15-25℃(温差±2℃影响管材圆度)
3. 停机规范
- 逐步降速至停机(避免螺杆抱死)
- 模头拆卸温度需降至80℃以下
- 清理时使用铜制刮刀(硬度<螺杆钢材)
三、90%操作者易犯的5大误区
- 忽视原料预处理:未对PP颗粒进行60℃/4h烘干,导致管壁气泡
- 过度依赖自动模式:未根据环境湿度调整真空度
- 错误判断堵料征兆:将电机电流波动误认为电压不稳
- 暴力处理粘模:用钢刷清洁导致模唇损伤
- 忽略设备振动监测:未发现减速箱轴承磨损初期征兆
某建材集团引入AR辅助操作视频后,新员工培训周期从45天缩短至18天,设备故障率下降37%。其视频特别标注了振动检测点(电机底座、齿轮箱连接处)和听音辨障技巧。
四、如何高效利用操作视频?
- 分段学习法:将2小时视频拆解为15个知识单元
- 场景化记忆:结合本厂设备型号建立参数对照表
- 虚实结合训练:在VR模拟系统重复练习紧急停机流程
- 建立错题集:记录实操中与视频标准的偏差项
某德国品牌挤出机的智能教学系统,能通过视频分析操作者动作,实时提示手腕角度偏差、工具拿取顺序错误等细节问题。这种将操作视频与AI结合的新模式,使关键工序达标率提升至99.3%。
五、进阶提升路径
当掌握基础操作后,可重点研究:
- 螺杆结构优化:渐变型vs突变型螺杆的产量差异
- 共挤技术应用:如何实现PP/PE双色管同步挤出
- 能耗控制策略:变频器参数与熔压的联动调节
一组对比实验表明:操作者观看带热成像分析的进阶视频后,能耗管控水平提升41%,这在当前双碳政策下具有特殊意义。